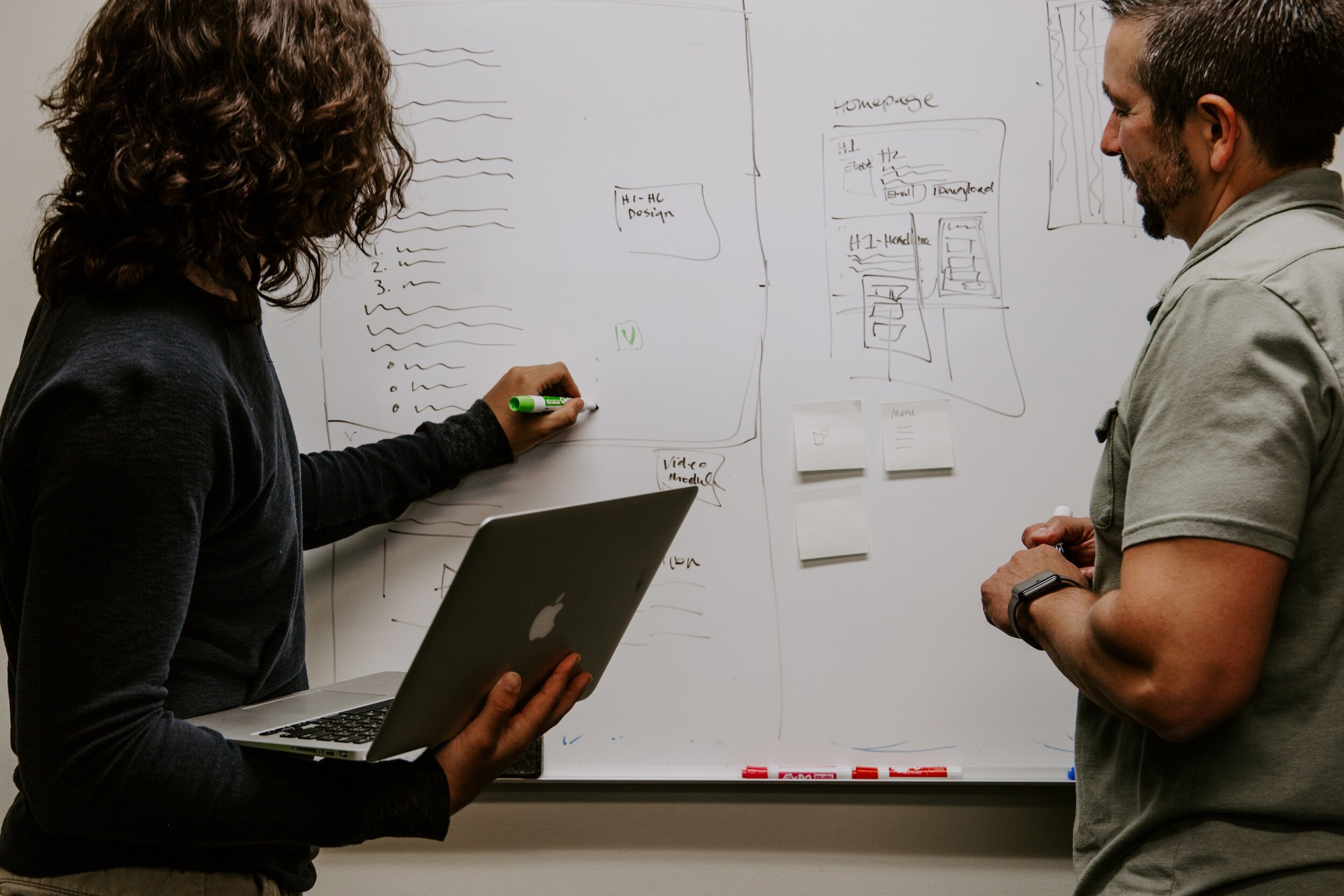
HOW WE WORK
WORK WITH HBI
There are a number of ways to work with HBI:
1) You are looking for a new soft goods or leather manufacturer. You either have a new product that has already gone through development (designs, patterns, sampling etc.) and is ready to be handed off to manufacturing, or, you are already in the manufacturing phase and are simply looking for a new source.
In both of these scenarios, an introductory call is needed to determine the scope at hand. In most cases, a sample will still be needed. This is to ensure we are capable of making the product, as well as properly determine the cost. Contact us to get the ball rolling.
2) You are interested in one of our other services offered. This includes marketing/design, kitting and assembly, and 3PL solutions. As with anything, an introductory call is required in order to determine scope. Contact us to learn more.
3) Finally, you are in need of product development/prototyping. Basically, you have a great idea and you’re ready to share it with the world. Or, you’re already a business that’s looking to launch a new product. In either case, below is the 10 phase approach we take for product development.
THE 10-PHASES OF PRODUCT DEVELOPMENT
PHASE 1: INTRODUCTIONS / MEET THE TEAM
First things first…introductions. The goal here is to make sure we are the right fit. With that being said, we first want to get to know you. During this phase, you’ll get to know your project manager, designer, and sample maker.
We’ll also talk through project specifics. This includes anything and everything you’re willing/able to share: goals, intended use, materials, design files/drawings if you have them, mood boards (which we highly recommend), MOQs, timing requirements, etc.
PHASE 2: PROJECT ESTIMATE
At this phase, we’re taking all that we have gathered so far and developing an estimated cost to develop the product. Estimates can be tailored to your specific requirements, but for the most part will include all the activities mentioned in the upcoming phases (1-8): concept, sourcing, pattern, sample, and manufacturing preparedness.
PHASE 3: CONCEPTING
Through multiple fact finding discussions, we’ll start nailing down all of the relevant details needed to create your prototype. This will include digital drawings to ensure the proper design/style/colorways are met, as well as verifying all known requirements to affirm proper fit and functionality. We will also suggest types of hardware and other raw materials as identified in the fact finding sessions.
PHASE 4: SOURCING
Now that we have a general concept, we’ll sit down and discuss all of the materials required to complete the sample. We may have touched on this in the concepting phase, but now is the time to really nail it down as well as the sources that will be used. We work with many different vendors, mills, and tanneries. We’ll show you all the options, order in swatches as necessary, etc. We’ll also talk through cost, as materials expense will play a significant roll in your overall, all-in cost to manufacture.
PHASE 5: PATTERN DEVELOPMENT
Pattern development is an iterative process and a required baseline for most product development/sample making. Please note that a pattern is seldom perfect on the first draft, so expect a round or two of changes/adjustments.
PHASE 6: SAMPLE MAKING
Similar to pattern making, expect an iteration or two. We’ll start by making a rough sample to test fit and functionality. Once we have an initial sample that works and is approved, the actual raw materials will be ordered and a final sample is then made that represents the exact product that you will be presented with.
PHASE 7: FIRST SAMPLE + CORRECTIONS
During this step, we review the sample and address any changes/corrections that need to be made. All aspects of the sample are discussed, noted and confirmed. We strive to accomplish this in one round of corrections but understand this is not always possible.
PHASE 8: FINAL SAMPLE PRESENTATION
A final sample is now presented for final approval and sign off. If approved, we begin preparing you for manufacturing. If the sample requires additional work/changes, we’ll take a step back and make the identified corrections.
PHASE 9: MANUFACTURING PREPAREDNESS
We start preparing you for manufacturing. When complete, you’ll have what you need to move the project forward. We will also supply you with a final quote to manufacture. Additionally, you’ll receive a bill of materials (BOM) which includes a list of all items needed (as well as the quantities) to manufacture the product.
PHASE 10: MANUFACTURING
If you decide to move forward with manufacturing, we will move forward with developing a tech pack. A tech pack is an instruction manual for the product being made which ensures all elements are included, as well as properly constructed.
We will also conduct a kickoff meeting at which time we discuss the scope of the project. This includes expectations, requirements and timelines.
In order to get started, we require half down (non-refundable). This will take you through phase 8. A final invoice will then be generated when the project is complete. This will include the remaining work (phase 9 and 10) + plus materials + freight if applicable.
**Please note– we cannot provide a cost for production until we have made a sample. There are times we can give a best guess, but without making a sample, it’s just that— a best guess.
**Project work is non-refundable.